光学相干成像技术在激光加工过程实时监测与控制中的应用研究进展
论文导读:本文主要内容来源于以下论文,以及相关行业研究报告,文章仅做通俗性解读汇总,如需深入了解还望观摩原文:
[1] 梅雪松,孙涛,赵万芹等.光学相干成像技术在激光加工过程实时监测与控制中的应用研究进展[J/OL].机械工程学报,2023(15):216-231[2023-09-10].http://kns.cnki.net/kcms/detail/11.2187.TH.20230811.1904.010.html.其余引用不一一列举,皆出自此文,如有需要,可微信后台领取。
论文摘要:
激光加工技术,主要包括激光焊接、激光增材和激光减材(切割、清洗、打孔等),具有高加工质量、效率、非接触等优点,在航空航天、生物医疗、通讯电子等领域应用广泛。随着产品精度与性能要求的逐渐提升,对激光加工的精度、效率及可控性提出了更高要求。因此,激光加工过程实时监测及调控成为了当前的研究重点。相比于传统的光声热电传感监 测,光学相干成像技术可以与激光束同轴耦合,从而直接获取激光加工结构的尺寸和形貌特征,具有高成像速度、高测量分辨率以及长测量范围等优点,被广泛应用于激光加工过程实时监测中。
本文系统介绍了光学相干成像系统的基本组成、成像原理,在此基础上综述了光学相干成像技术在激光焊接、激光增材制造和激光减材制造实时监测与控制中的应用。 最后,归纳了目前光学相干成像技术在激光加工过程监测中存在的不足和发展趋势,为激光加工过程实时监测与控制的研究工作提供了坚实基础和发展方向。
OCT系统组成及成像原理
OCT系统组成
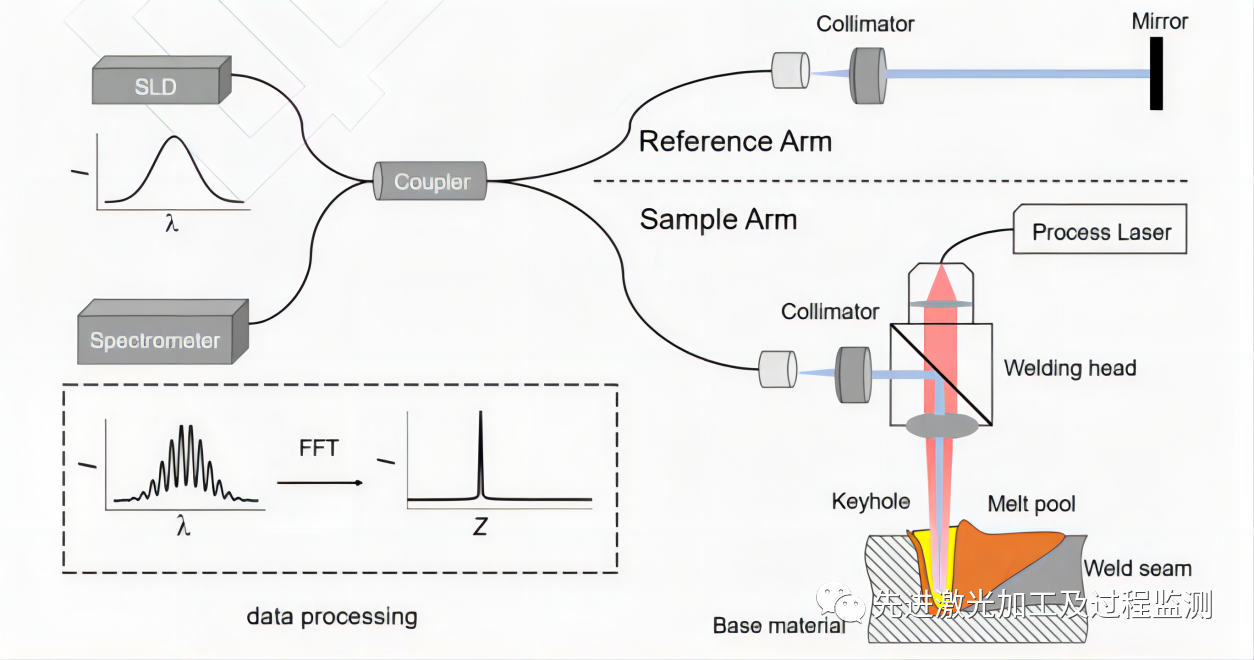
图1 OCT熔深监测原理图[2]
OCT(optical coherence tomography)熔深监测系统通过将样品光和激光焊接光路进行同轴耦合,根据宽谱光源的相干性来获取匙孔深度信息。主要包括超辐射发光二极管SLD,光纤耦合器,参考臂,样品臂和光谱仪等部分。其中,参考臂由偏振控制器,光纤准直器,色散补偿片,反射镜等构成,样品臂通过光纤准直器与激光焊接光路进行同轴耦合,使得样品检测光与加工激光中心同轴对准,以便在焊接过程中进入匙孔底部对深度进行测量。
根据不同的传热模式和是否产生小孔,激光焊接分为热导焊和深熔焊。热导焊仅在金属材料表层发生熔化,形成熔池;当激光功率密度达到一定阈值时,金属材料表层发生气化,熔池在气化反冲压力的作用下向下凹陷形成深熔小孔,这种焊接模式被称为深熔焊,是激光焊接领域主要采用的焊接模式,OCT技术路线做熔深检测时仅适用于深熔焊。
OCT成像原理
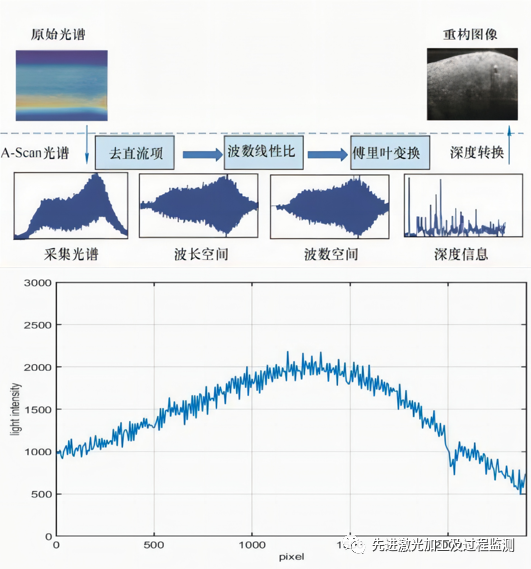
图 2 数据处理流程(上);干涉信号图(下)
光的干涉指的是;当几列光波在空间相遇时,部分光波叠加区域光强始终得到加强,而某些叠加区域光强始终被削弱,从而发生稳定的强弱分布的现象。
谱域OCT检测系统主要是通过分析采集到的干涉频谱来获取深度信息。在理想状态下,采集到的光谱信号应该是延 Z 轴方向排列的 n 个高斯峰,高斯峰的宽度即为该系统的轴向分辨率,具有不同的反射率和深度的响应点对应一个高斯峰,干涉光经过光谱仪的光栅后,分布在线阵CCD 上,根据定标得到的 CCD 像素点对应的波数关系,利用快速傅里叶变换得到不同的干涉光谱对应的深度信息,再利用扫描振镜控制扫描镜头沿 X、Y 轴方向移动即可得到表面轮廓的三维信息。
OCT系统性能指标-关键参数-轴向分辨率
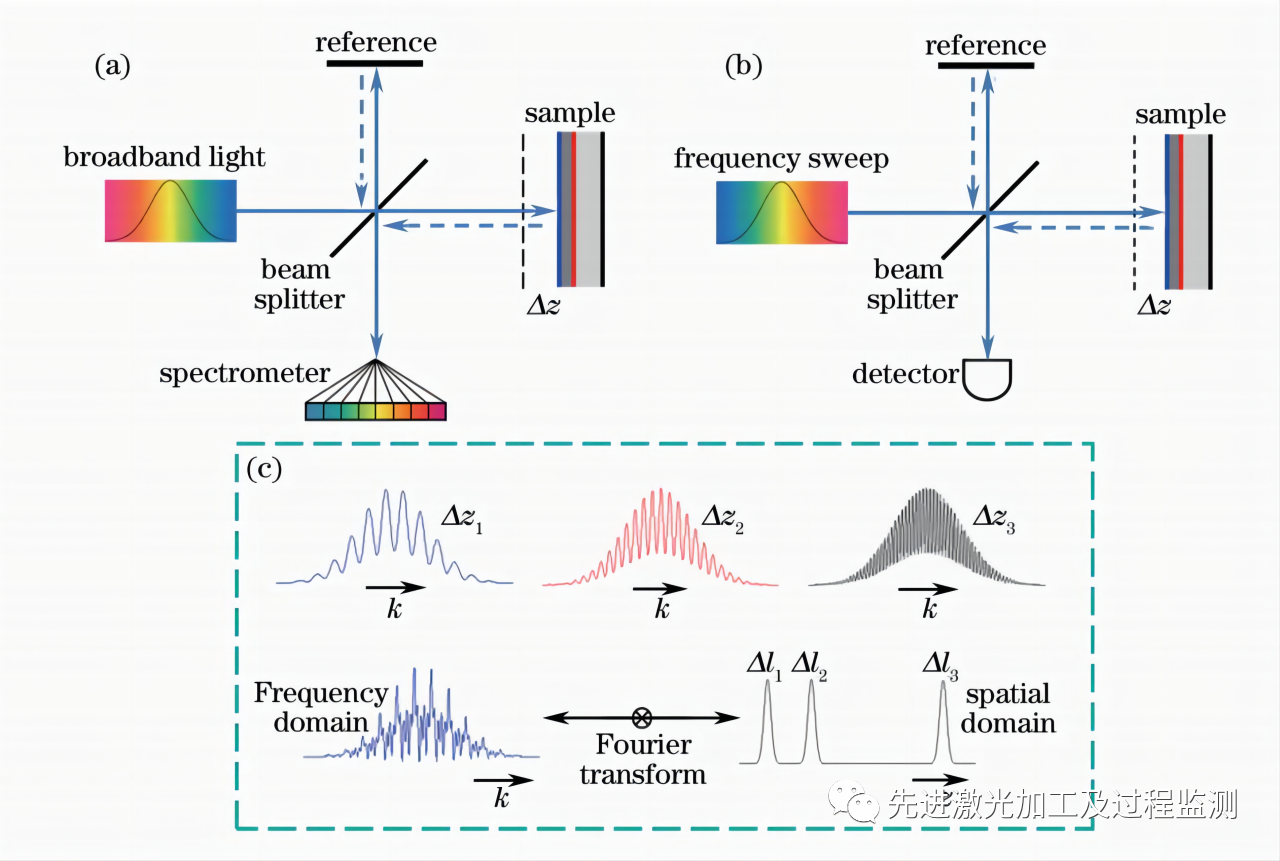
图3低相干干涉傅里叶域探测示意图[3]
线阵 CCD 采集到光谱强度是沿 z 轴方向排列的高斯峰,不同的高斯峰代表了具有不同深度的反射点(测量点),当两个不同波长的高斯峰极点距离小于高斯峰的半高长度时,在图像上会表现为一个两者叠加的高斯波形,此时便无法区分这两个高斯峰所代表的对应点。所以一般将光谱信号进行傅里叶变换后的半峰宽作为 OCT 系统的轴向分辨率。
一般采用光源中心波长为 850nm,光源半极值全宽度为 40nm 则系统理论轴向分辨率为 8µm,但实际搭建的OCT 系统受到色散等因素的影响,实际轴向分辨率要大于理论计算的数值。
OCT系统性能指标-关键参数-横向分辨率
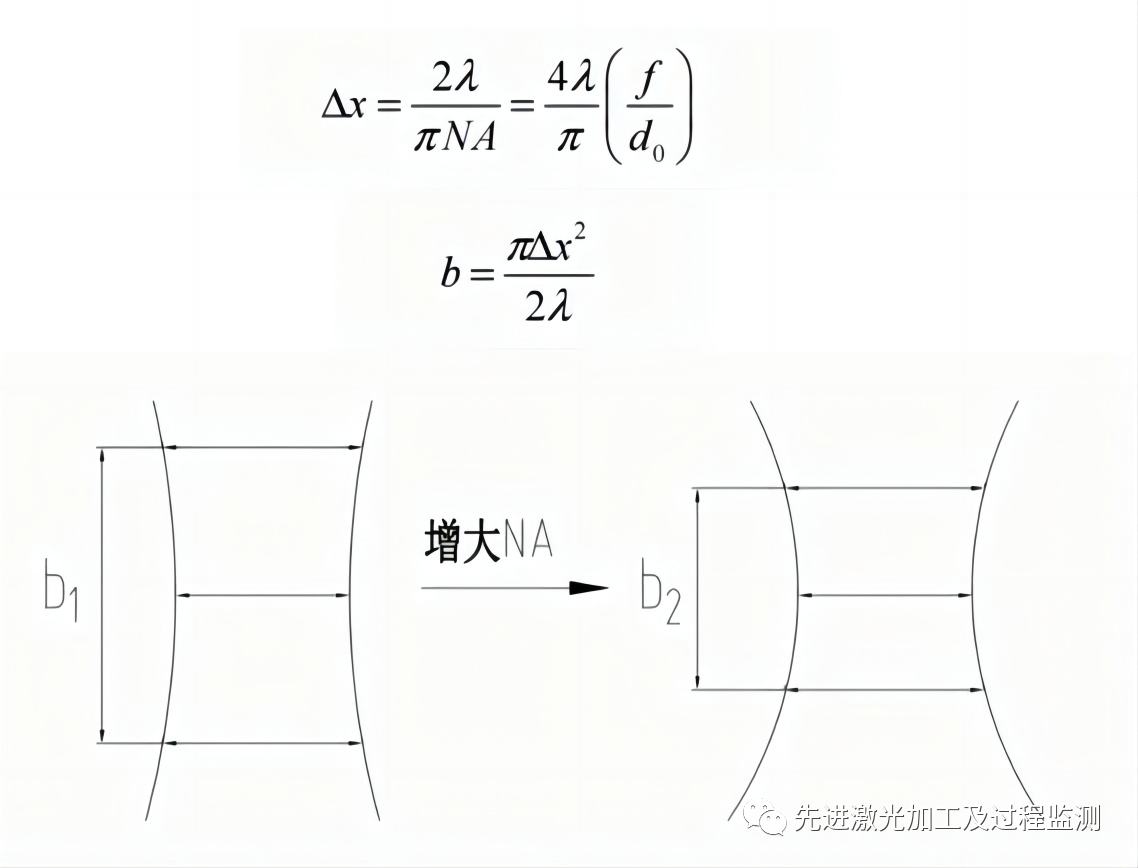
图4 分辨率计算公式
OCT 系统的横向分辨率独立于轴向分辨率,横向分辨率主要取决于聚焦物镜的数值孔径和投射到待测物表面的光斑的尺寸。其中△x 为分辨率,f 为聚焦物镜焦距,d0 为物镜通光口径、入 为波长,NA为数值孔径,b 表示焦深。从公式可以看出,通过增大焦距、降低物镜通光口径、增大数值孔径NA,可以提高横向分辨率。但在实际搭建时,需要考虑聚焦光学系统的焦深。当光学系统焦深减小,即聚焦光学系统的有效工作深度会减小,如图所示,当部分待测物不在焦深范围内时,光学系统采集到的图像横向分辨率较差,所以在实际搭建 OCT 系统的过程中需要根据工作要求合理选择系统参数。
OCT系统性能指标-关键参数-成像深度
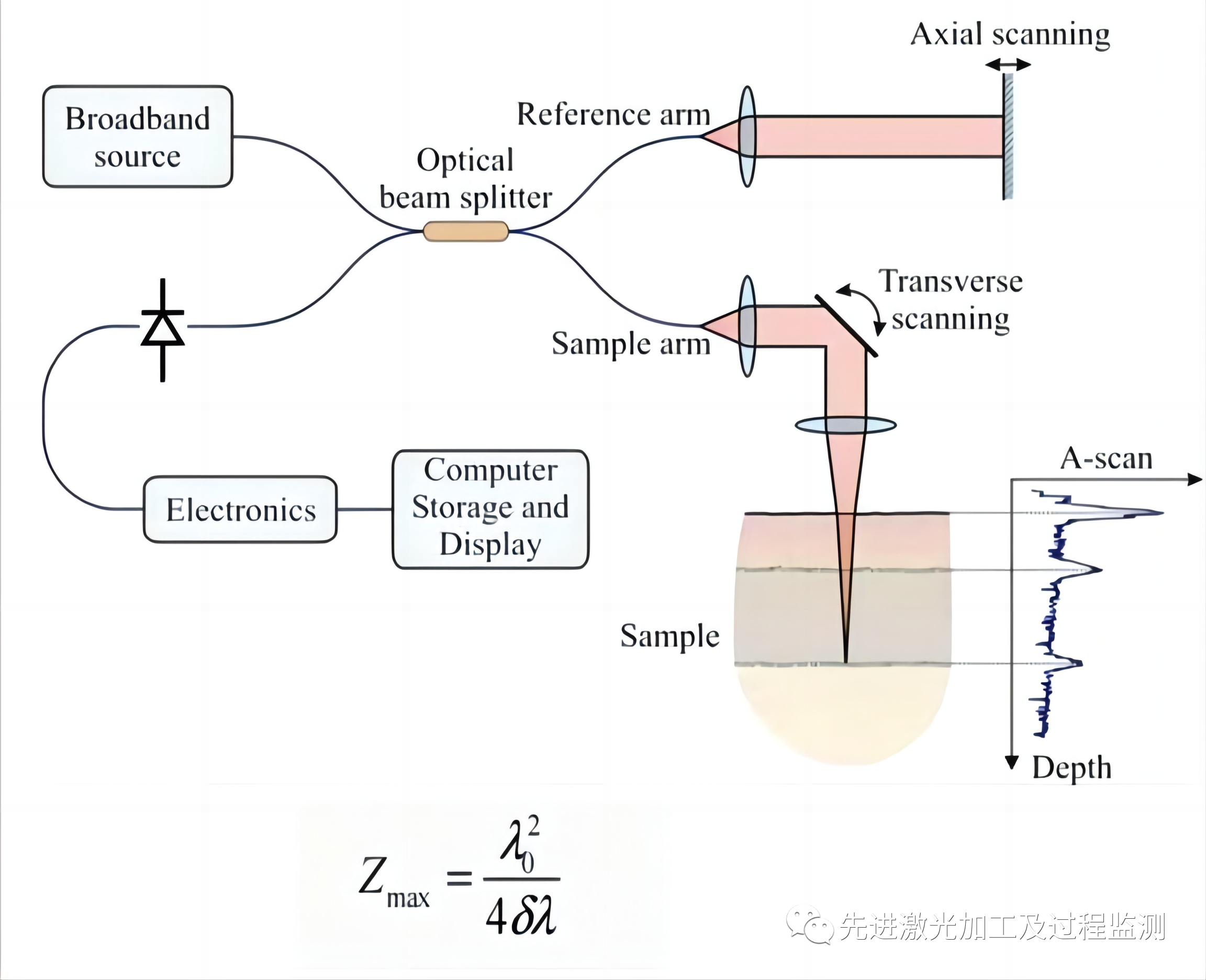
图5 OCT成像深度示意图
谱域 OCT 检测系统成像深度主要受光源中心波长、光谱宽度、以及光谱仪的分辨率等因素影响。
光谱仪的光谱分辨率为δλ,从公式可以看出谱域 OCT 系统的成像深度主要取决于光谱仪的分辨率,可以通过提高光谱仪的成像分辨率,增大检测系统的成像深度。
OCT系统性能指标-关键参数-成像速度
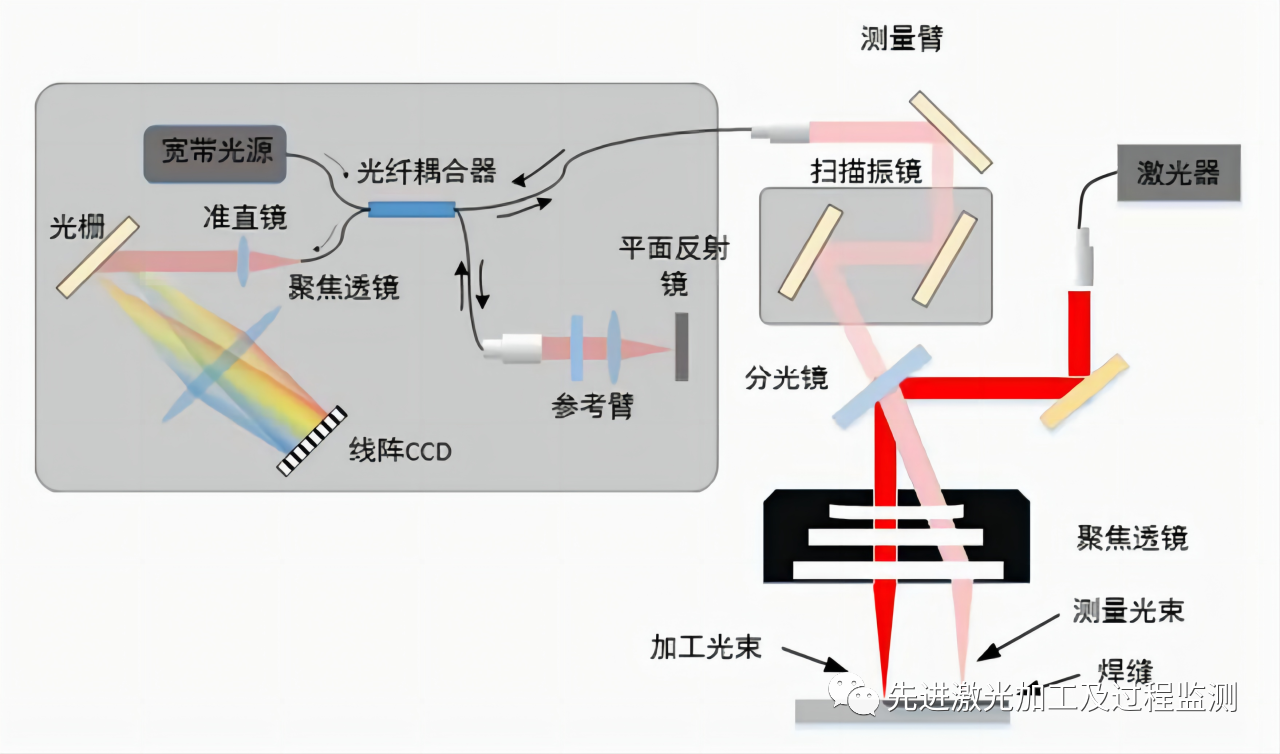
图6激光焊接质量在线检测系统原理图[4]
谱域 OCT 系统成像速度主要由高速线阵 CCD 相机成像性能,横向扫描装置的扫描速度以及程序数据处理速度决定。现在主流线阵相机的采集速度一般在 10KHz-50KHz 左右,而谱域 OCT 系统一般利用扫描振镜完成横向扫描,其扫描速度最高能达到几百 KHz,可以轻松满足 OCT系统的扫描成像要求。系统需要对采集到的光谱信号进行线性插值、傅里叶变换,才能得到所需的深度信息,所以系统的数据处理速度是限制谱域 OCT 系统扫描成像速度的主要因素。
基于OCT监测技术研究现状
OCT监测研究现状
基于 OCT 的激光焊接过程实时监测可以直接获取加工中焊接熔深及焊缝截面形貌,更便于观察、控制焊接过程中的匙孔稳定性,降低外界干扰对焊接过程的影响,在焊接质量控制方面具备显著优势,在学术研究领域和应用市场都涌现了大量成果。

图7 IPG-LDD激光焊中监测
首先最为众人所熟知的就是加拿大女王大学的 PAUL 和 JAMES 等提出的内联相干成像(Inline coherent imaging, ICI)正式打开了 OCT 在焊接过程监测中应用的大门,其将 OCT 集成至激光加工装置中,令检测光与加工光同轴进入加工区域,并将这种 OCT 与加工光同轴探测的方法命名为ICI ,同时也基于该技术创建了 Laser depth dynamics (LDD) 公司,并与2017年被IPG收购,当前已更新到LDD-700系列,应该是当前技术最为领先的OCT工业检测产品。
OCT监测研究现状-熔深闭环控制
同时德国汉堡工业大学的 NEEF等联合普雷茨特公司的研究人员将低相干干涉测量仪集成到激光选区熔化(Selective laser melting, SLM)装置中,可用其来区分粉末结构和SLM成形结构,从而减少送粉过程中粉末缺失或减少以及粉末沉积在零件表面对零件成形质量的影响;其还可以用于重建 SLM 零件的表面轮廓,以监测到零件的隆起和变形缺陷。
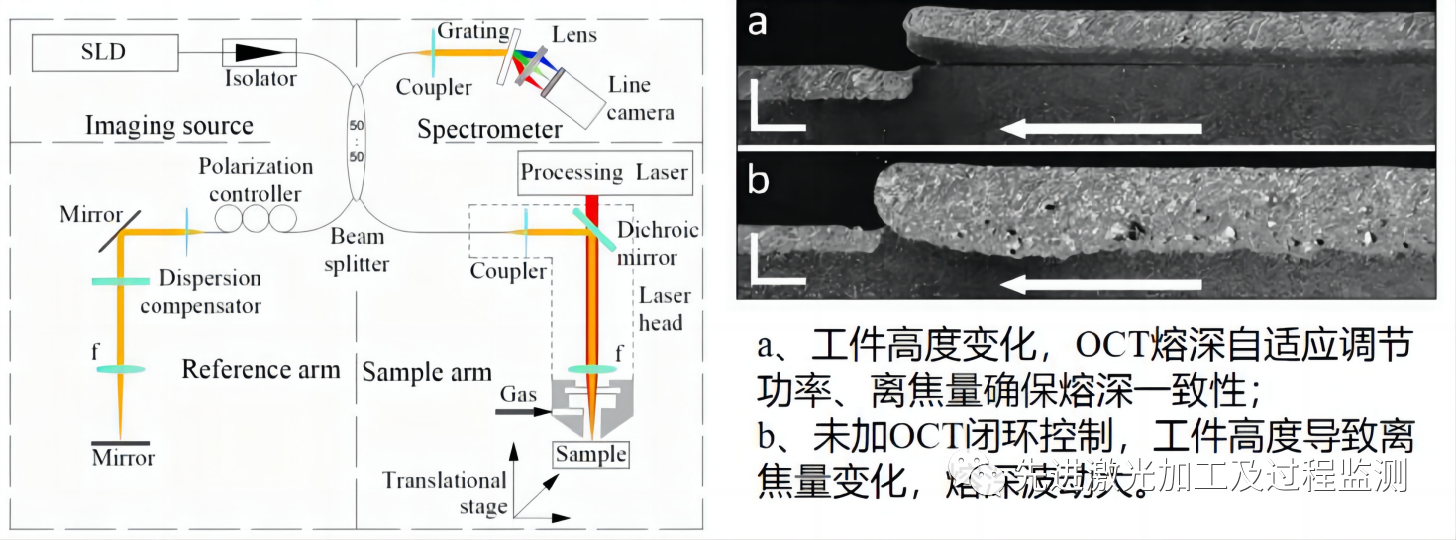
图8 OCT熔深闭环示意图
学者研究了通过 OCT实时监测焊接过程中的熔深,以反馈控制功率、离焦量以实现焊接过程中的恒定熔深,并且其展现了该技术在不同合金焊接过程中实时测量匙孔深度的能力,并且利用该种方法研究了匙孔的产生和演变过程,可用于探索激光焊接过程机理。
OCT监测研究现状-工艺对比优化
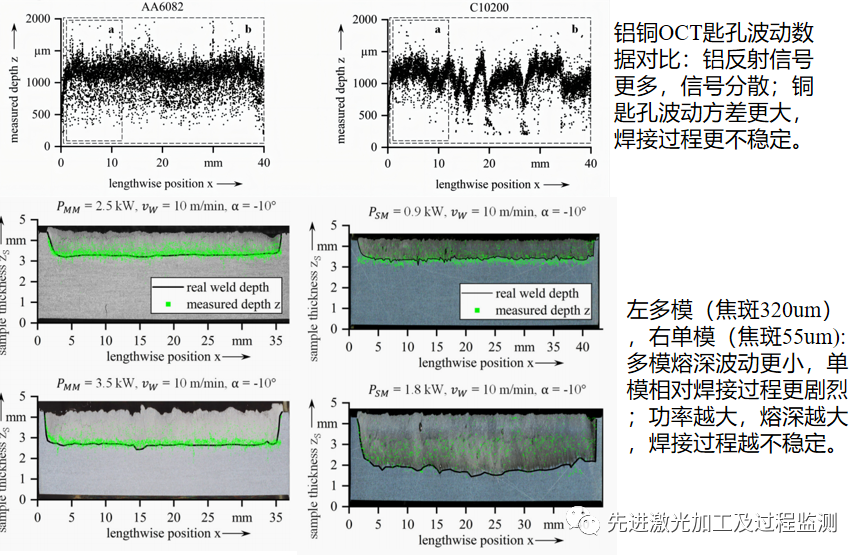
图9 OCT熔深监测铝铜对比图
此外,为探索加工过程工艺参数对 OCT 信号的影响,德国慕尼黑工业大学机床与工业管理研究所的MICHAEL 课题组系统地比较了不同加工材料、入射角度、焊接深度等参量下 OCT 信号的差异,结果表明不同材料焊接过程形成的匙孔会对 OCT产生不同的反射作用,且随着焊缝深度的增加,匙孔波动会更加明显,铝散射比铜剧烈;铝焊接过程比铜稳定、匙孔深度波动小;焊接光斑越大越稳定(多模稳定性好于单模);焊接头后倾比前倾焊接过程更稳定。
OCT监测研究现状-质量评价
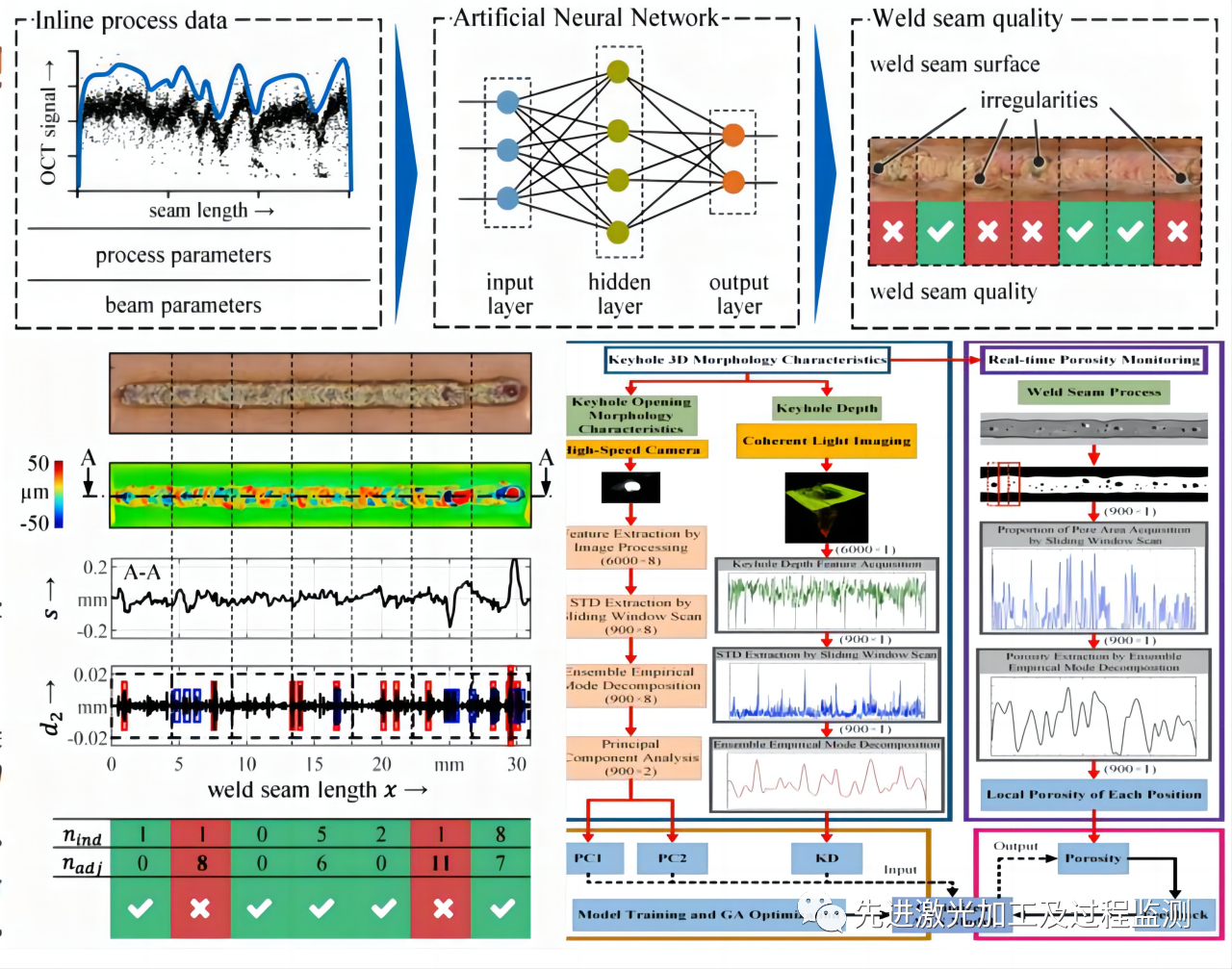
图10 基于OCT的激光焊接质量判断示意图
同时也有学者探索了 OCT 信号在评估焊接质量方面的应用。其利用 OCT 对深熔焊匙孔深度进行了测量,将 OCT 测量结果与焊缝表面质量分析结果进行比较,并利用机器学习建立焊缝深度信号与焊缝表面质量之间的相关性,由此可以利用焊缝深度信号来预测焊接过程的表面质量。华中科技大学的 MA 等基于 LDD 的光学相干成像系统对焊接过程中匙孔进行了测量,其可以直接重建出加工过程中匙孔的三维形貌,以此量化匙孔的波动性,并通过提取匙孔的关键信息特征,可以定位到激光焊接过程焊缝中的气孔位置,并实现了对焊接件孔隙率的预测。
OCT焊接、增材、减材制造应用
OCT焊接应用—激光焊接工业应用
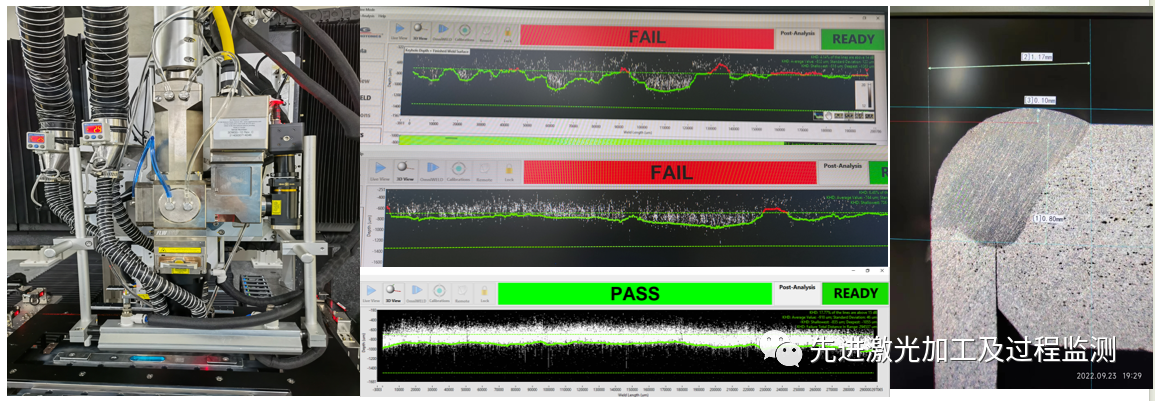
图11 基于OCT的IPG-LD用于动力电池顶盖满焊
动力电池顶盖满焊熔深检测应用:识别局部熔深不足,超限。主要应用与对熔深要求较高的场景、电池相关零部件焊接:BUSBAR、软连接、连接片、防爆阀、极柱等;汽车零部件:座椅、安全气囊压力容器、差速器等;
OCT增材应用
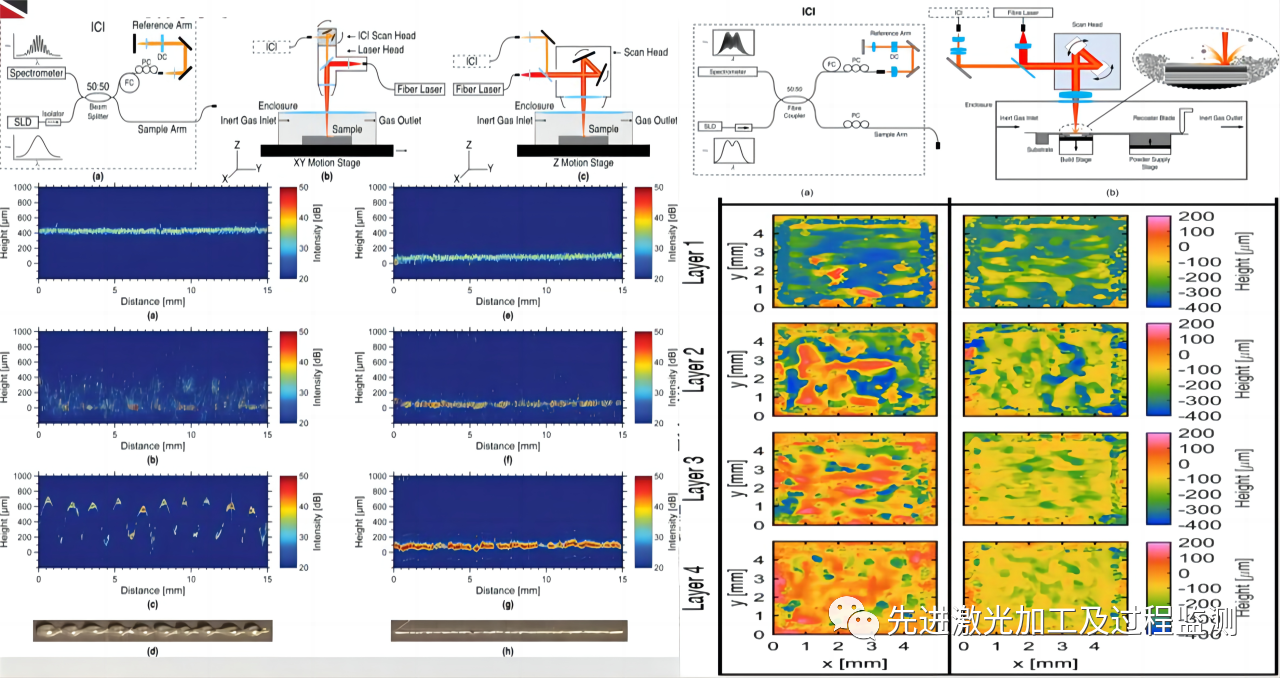
图12 基于OCT增材外观高精度监测示意图
除了获取熔池深度以外,OCT 在激光增材制造过程监测中的应用主要侧重于层三维形貌的获取以及加工过程的缺陷监测,其可以直接获取加工过程中表面粗糙度和缺陷,从而优化加工质量;由于其可以实现加工过程各层形貌的重构,因此其还可以用于研究加工过程的形貌演化过程,以阐明加工过程缺陷产生机制。
左图为实时监测 SLM 过程中的熔池演化动态案例,通过对 SLM 过程的熔池截面进行实时成像,可以识别加工过程中的液固相变区域及熔池长度区域,并且可以对加工过程中粉末、熔池、基底及凝固区域进行区分,可以用于检测工艺缺陷,还可以用于探索不同工艺参数下的熔池形貌动态,用于评估各种工艺参数对加工质量的影响,更有效的调整和优化参数。同时针对多层增材叠加时可获取增材制造每一层处理前后的层厚以及如表面粗糙度、粉末堆积密度等形貌信息,进而可以实现工艺参数的闭环控制,以消除增材制造过程中的突起和凹陷,降低最大粗糙度,为增材制造过程中的实时优化和闭环控制提供了基础。
OCT减材应用
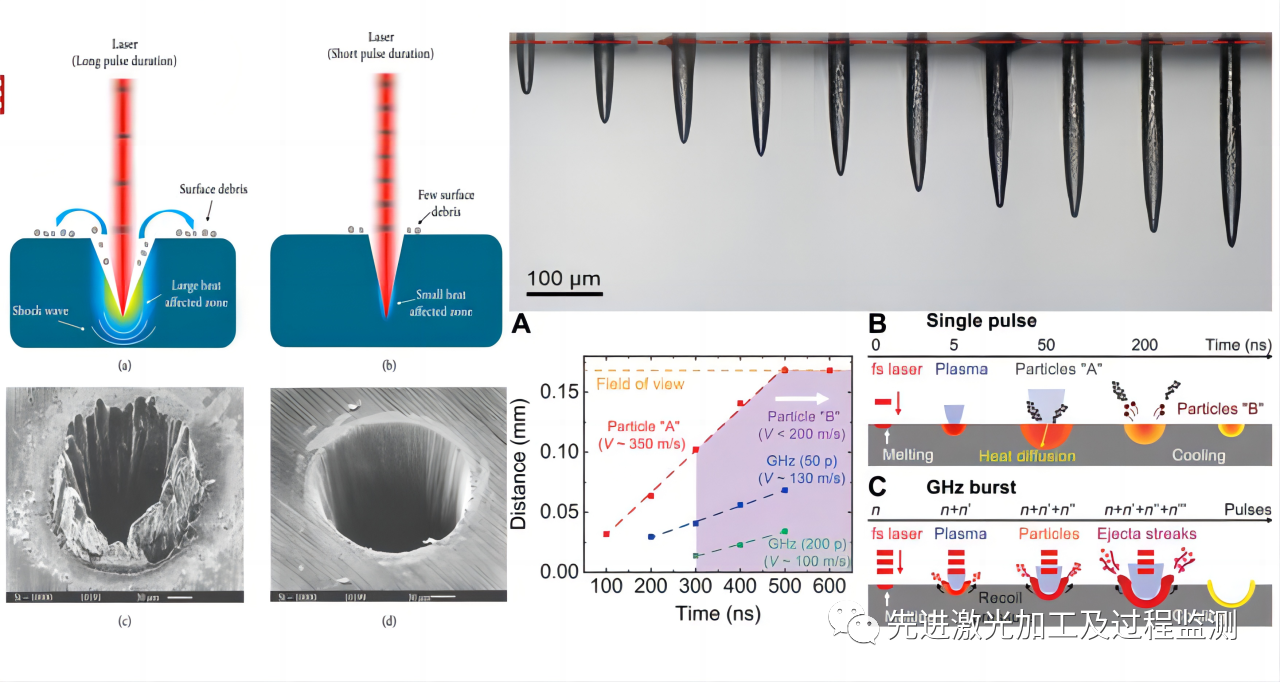
图13 基于OCT的激光转孔检测示意图
减材制造是相对于“增材制造”而言,通过对材料进行去除来使工件获得规定的几何形状、尺寸和表面质量的加工方法都可以称为减材制造。而激光减材制造主要包括激光切割、打孔、抛光及表面刻蚀等多种加工方式。与激光焊接、增材制造不同的是,上述加工方式大多采用的连续或长脉冲光源,其加工过程热效应明显,容易产生大量的缺陷。而目前的激光减材制造所用光源逐渐向飞秒激光发展,其加工具有高精度、极小重铸层和热影响、非接触等显著优势,目前被广泛应用。
然而,由于激光的高斯分布及其传输特性,其在加工盲结构(如盲槽、盲孔)、多层材料中的表面结构去除(如碳纤维表面涂层、天线薄膜等)以及带中空腔体材料的切割、钻孔(如涡轮叶片、喷油嘴等)时往往容易出现过烧蚀,导致底部不均匀或过度烧蚀,由此影响加工质量。而 OCT 可以实时获取加工位置的深度信息,由此实时控制加工深度,可以避免由加工过程波动导致的底部不均匀。并且其还可以监测不同材料界面之间的变化,用于定量控制对单层材料的烧蚀,避免过烧蚀的出现。
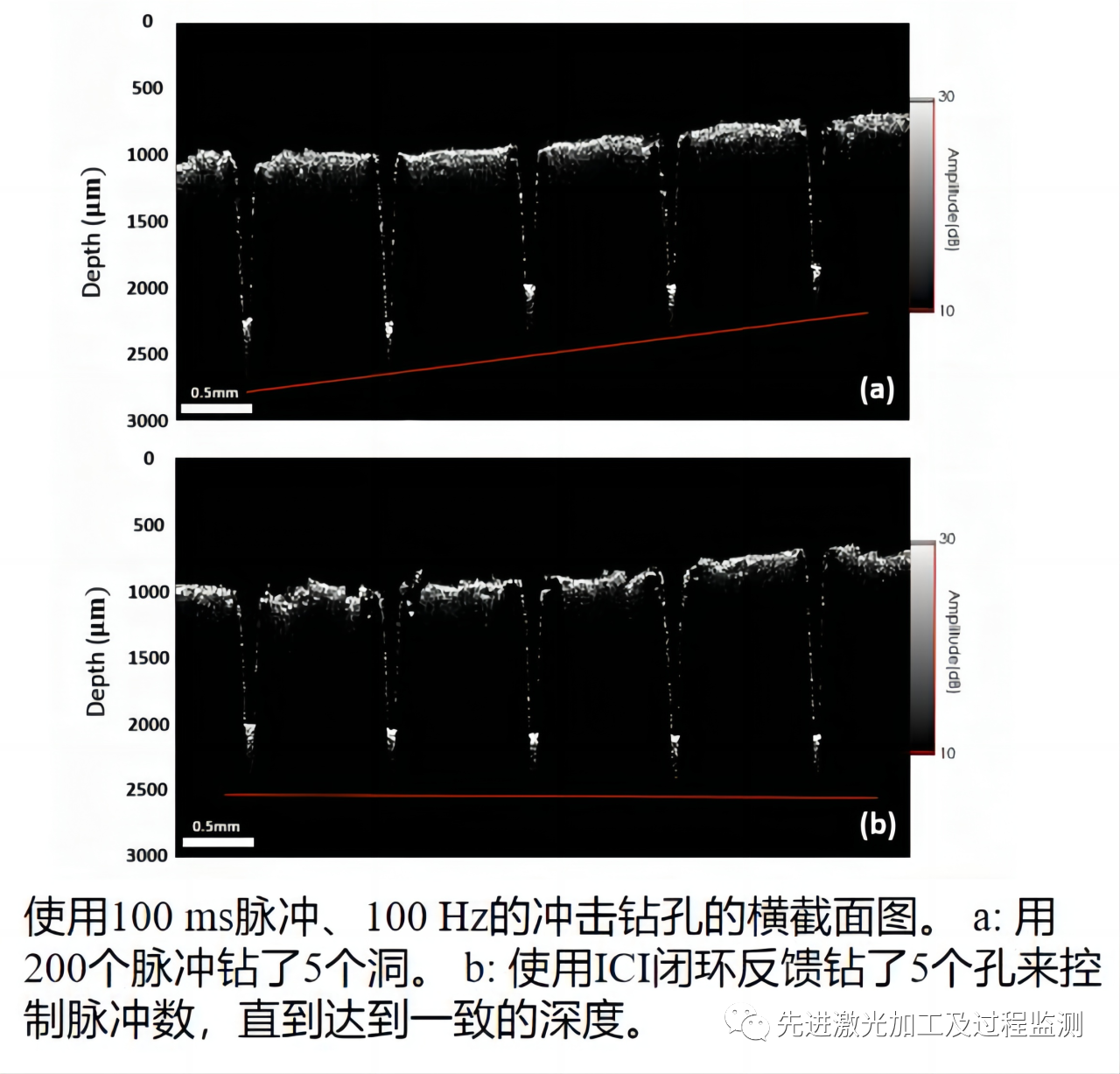
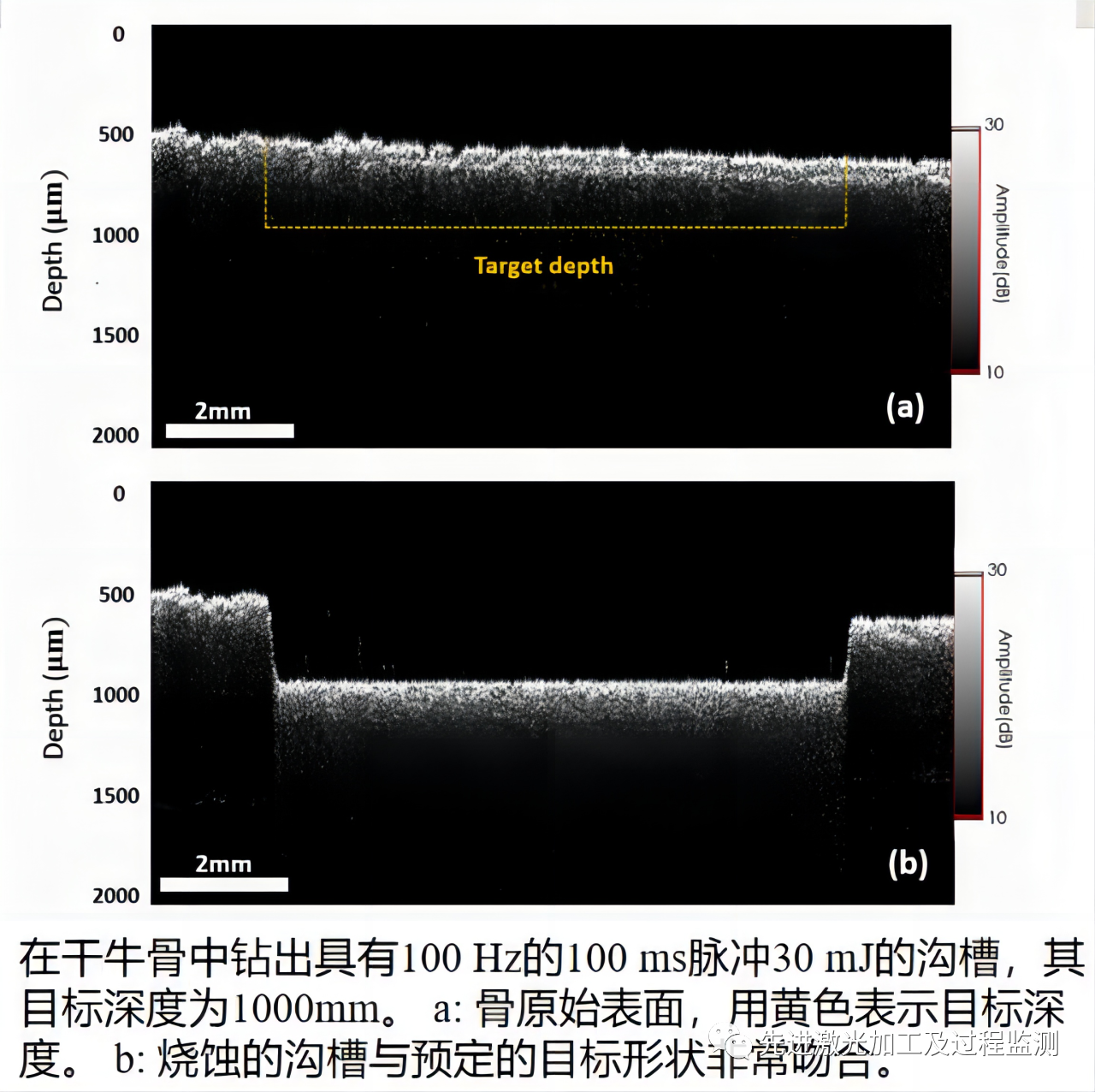
OCT在超快激光打孔、刻蚀过程中的实时测量深度和截面形貌,实现了激光加工过程孔深的实时测量与反馈,生物组织激光切割和制孔深度的实时测量与控制,并且将其集成至扫描振镜中,可以快速实现对沟槽截面形貌和三维表面形貌的重构和反馈控制。总的来说:OCT 在激光减材制造中的应用目前主要集中于超快激光切割、制孔、表面刻蚀等应用,用于实时测量激光烧蚀深度或三维形貌,以实现对烧蚀深度的精确控制或质量的优化。
OCT相关产品
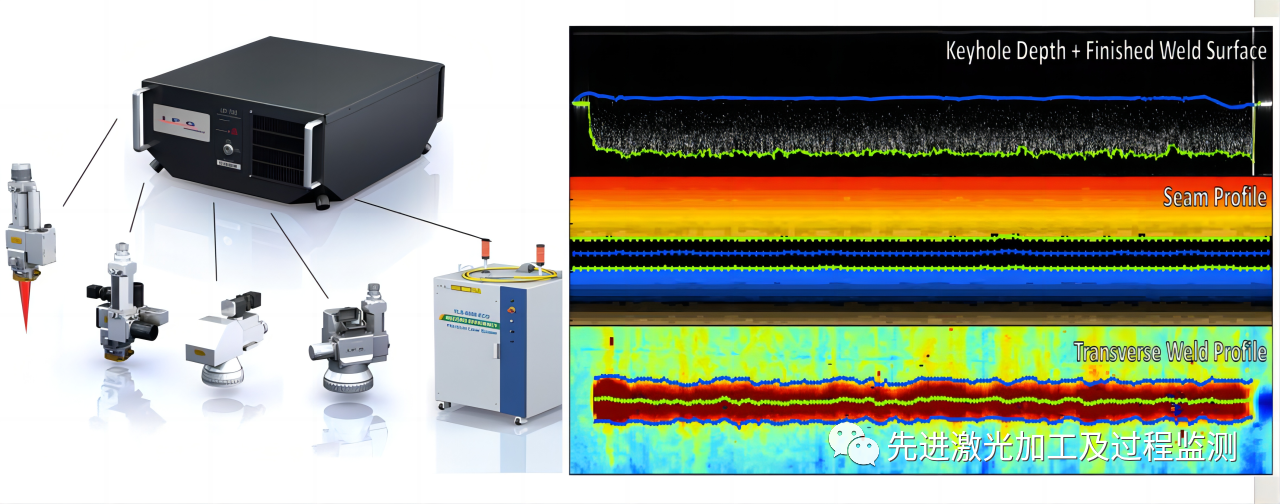
图16 基于OCT的焊中监测产品 IPG-LDD
当前相对成熟的OCT检测产品当属IPG-LDD-700,OCT应用到激光焊接上涉及到对激光工艺机理层面的深层次理解、涉及对整个焊接光路的优化、涉及对振镜控制系统的开发,有句话怎么说的来着:设备只是公司对工艺认知的体现——来自宝利苏迪,OCT监测也是如此。
OCT技术趋势
整体来说,OCT 技术在激光加工过程监测领域具有广阔的应用场景:一方面, OCT 可以直接实时获取加工过程的深度及形貌信息,能够帮助我们实时控制并优化加工质量,定位加工缺陷;另一方面,利用 OCT 对加工过程的深度或形貌信息进行实时成像,可以帮助我们理解整个加工过程的演化过程,以探究激光材料相互作用机理与缺陷形成机制。而从目前的国内外现状来看,国外研究机构已开展相对较多的研究,并且已经形成商业化仪器产品,在激光焊接领域开始展开使用。而国内的研究近几年刚刚开始,目前还处于起步阶段。光学相干成像在激光加工过程监测的应用还处于初级阶段,还有许多理论和技术难题亟需进一步研究。为实现更快速、更微观、更全面、更精准和更智能的激光加工过程在线监测与控制,应仍需进一步加强 OCT 技术与加工在线监测技术的融合,探索高成像速度、数据处理速度和分辨率的 OCT 成像技术,并引入多传感、多信息进行融合监测,对激光加工过程进行全方位监控,并进一步结合人工智能方法建立状态监测模型,从而实现对加工状态、缺陷的智能化监测和精准控制。
OCT监测从医学技术外溢到工业的过程刚刚开始,还有很多工作需要做,技术还有相当大的发展进步空间,希望越来越多厂家关注到、投入到相关研究当中,推动行业向前发展。
声明:
1. 本文素材部分来源于网络,如有侵权,请联系删除;
2. 随着锂电、光伏、激光器的发展、越来越多的工程师开始接触到激光,考虑到激光工艺是个极其依赖实操的技术,当前市面上缺乏相关的学习资料,本公众号旨在传播相关激光工艺应用的相关基础知识,推进行业向前发展,在此特向工艺同行呼吁,如有志同道合者,欢迎整理您的工艺经验、对激光的认识,联系我投稿,帮助更多的工艺同行,在此一并感谢;
3. 本公众号建有相应的激光工艺交流群,欢迎工艺同行加群交流,互相学习。
另附部分涉及文献:
[2]谢冠明,王三宏,张跃强等.基于光学相干层析的激光焊接熔深监测方法[J].光学学报,2023,43(11):146-156. [3]李培,杨姗姗,丁志华等.傅里叶域光学相干层析成像技术的研究进展[J].中国激光,2018,45(02):153-163. [4]吕思航. 基于OCT的激光焊接质量在线检测技术研究[D].长春理工大学,2022.DOI:10.26977/d.cnki.gccgc.2021.000615.免责声明:本文旨在传递更多科研资讯及分享,所有其他媒、网来源均注明出处,如涉及版权问题,请作者第一时间联系我们,我们将协调进行处理,最终解释权归旭为光电所有。